How to shorten the cycle time without compromising the quality of high precision injection molding?
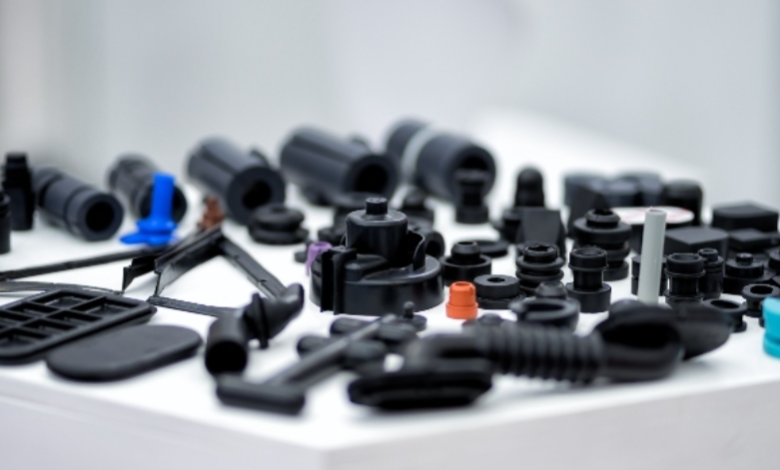
Shorter injection molding cycle times translate directly into increased productivity and cost efficiency, which are essential to meeting customer demands and staying competitive. However, speed should not come at the expense of part quality when performing high precision injection molding. This guide will explore proven strategies and advanced technologies to help you reduce cycle times while maintaining the stringent quality standards required for your products.
Optimizing Machine Settings for Faster, Higher Precision Injection Molding
The foundation for reducing cycle times lies in optimizing the injection molding machines. Every parameter, from injection speed to pressure setting, must be calibrated for high-precision injection molding to reduce cycle times while ensuring that the final product meets the required tolerances. Injection speed is one of the most critical parameters to control when reducing cycle times. You can increase the injection speed to help fill the mold faster, but you must do it cautiously. Injecting too fast can cause defects such as burrs, burn marks, or poor filling, which can affect product quality. The key is to find the optimal injection speed that ensures fast filling without compromising part quality.
In addition, setting the correct injection pressure is critical. The pressure must be sufficient to fill the mold cavity and compact the material, but too much pressure can cause problems such as part warping or material degradation. Applying pressure evenly and gradually in high precision injection molding can reduce cycle time without compromising quality.
See also: The Best Massage Techniques for Improving Posture
Improve mold design for high precision injection molding.
Mold design is a key component of high-precision injection molding and directly affects molding cycle time and product quality. Well-designed molds help eliminate bottlenecks in the injection molding process and reduce molding cycle time without compromising part accuracy. Manufacturers can optimize molds for better material flow and cooling by using advanced mold design techniques, significantly reducing molding cycle time.
One key design improvement is optimizing the mold’s cooling channels. Cooling time is one of the longest stages in the injection molding cycle, so reducing cooling time can significantly impact the overall cycle time. To enhance cooling, mold designers can use conformal cooling channels, which transfer heat more efficiently than traditional straight channels. These channels follow the shape of the mold cavity, ensuring more uniform cooling and reducing the risk of warping and dimensional inaccuracies.
Advanced Cooling Systems
Cooling is one of the most extended phases of a high-precision injection molding cycle, and optimizing cooling is one of the most effective ways to reduce overall cycle time. Conventional cooling methods typically use straight cooling channels, inefficiently removing heat from the mold. However, advanced cooling systems offer a more effective solution by improving heat transfer and reducing cooling time.
Conformal cooling channels are one such advanced technology. Unlike conventional cooling channels that run in a straight line, conformal cooling channels are designed to follow the contours of the mold cavity. This design allows uniform cooling across the entire mold surface, resulting in faster, more consistent cooling rates. This improvement can significantly reduce cycle time, especially for molds with complex geometries or parts that require rapid cooling.
Optimizing Injection Cycle Phases
In high-precision injection molding, optimizing each phase of the injection cycle is critical to reducing overall cycle time. The injection cycle consists of several phases: injection, holding, cooling, and ejection. Each phase affects cycle time, and optimizing these phases can reduce production time without sacrificing quality.
The injection phase is the first step, during which the machine injects material into the mold cavity. To reduce cycle time, manufacturers can increase injection speed, but it is essential to find the right balance to avoid overfilling or causing defects such as flash. Manufacturers can optimize this phase by adjusting injection speed, pressure, and holding time to fill the mold quickly and efficiently.
The holding phase follows the injection phase and is critical to ensuring that the part is fully packed and free of voids. This phase can be optimized by adjusting the holding pressure and time. Manufacturers can avoid underpacking the part and reduce cycle time by using the correct holding pressure and ensuring the material fills the cavity.
Intelligent Process Monitoring and Control
Implementing intelligent process monitoring and control systems is an effective strategy for optimizing high-precision injection molding. These systems provide real-time feedback on key process parameters such as temperature, pressure, and injection speed. By continuously monitoring these variables, manufacturers can make immediate adjustments to prevent defects and optimize molding, reducing cycle time.
Intelligence also helps to precisely control the injection molding machine, ensuring that each cycle is consistent. This eliminates variations that can cause defects or waste, improving the overall efficiency of the molding process. For example, an automated system can adjust the injection speed or pressure based on the mold’s temperature or the material’s behavior, ensuring that the system makes each shot with optimal parameters. Integrating sensors and data analytics also enables manufacturers to track process trends and identify areas for improvement. Over time, this data can be used to optimize machine settings, adjust mold parameters, and fine-tune cooling systems to further reduce cycle times.
Ultimately
The entire injection cycle stage can be optimized by optimizing injection molding machine settings, improving mold design, and using advanced cooling systems. Intelligent process monitoring and control can reduce cycle times without sacrificing the quality of high-precision injection molding.